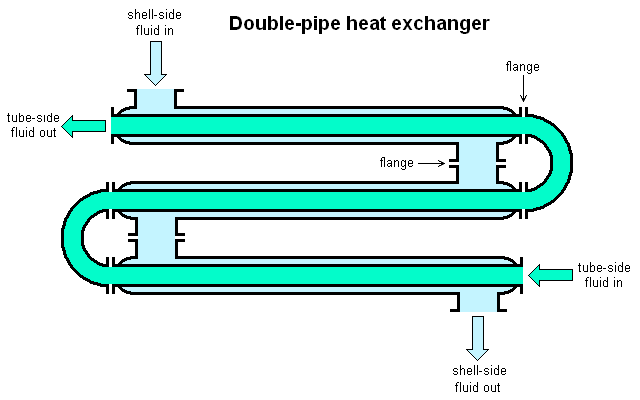
Heat Exchangers for Anaerobic Digestion Plants UK HRS Etc
Until recently Heat Exchangers were not thought needed for Anaerobic Digestion Plants. They have been a rare sight at Anaerobic Digestion (AD) Process Plants both in the UK, and worldwide.
Watch our video on this subject, below.
How It Was:
In the first generation of anaerobic digestion plants, the provision of Combined Heat and Power (CHP), beyond maybe heating the farmhouse and barns on a farm digester, was rare.
For the majority of these digesters, the diesel engine generator cooling jacket-heat was used to heat the digester substrate, and beyond that, there was little demand for highly efficient use of the hot-water (heat) energy left over from the electrical generation activity.
Hot water was circulated within pipes laid around the interior of the digester perimeter to provide a form of heat exchanger, however, these “heating pipes” are not even called “heat exchangers” within the biogas industry.
The Future:
That is all changing with the development of biogas-upgraded AD facilities to produce biomethane, in preference to the main purpose of the AD plant being to generate electricity for profitable export to the electricity network HV grid, true “high-efficiency heat exchangers” are becoming much more frequently used.
Given the above, in this heat exchangers for anaerobic digestion article we decided to round up some relevant recent web-based information on Heat Exchangers for Anaerobic Digestion Plants and include the most relevant, as follows:
HRS Heat Exchangers (and other companies) produce heat exchangers for use throughout the anaerobic digestion process, including:
- Exhaust gas cooling and energy recapture
- Feedstock and/or sludge heating
- Feedstock or digestate pasteurisation
- Digestate concentration and evaporation
- Thermal hydrolysis for enhanced gas production. via Biogas – Heat Exchangers for Anaerobic Digestion Process
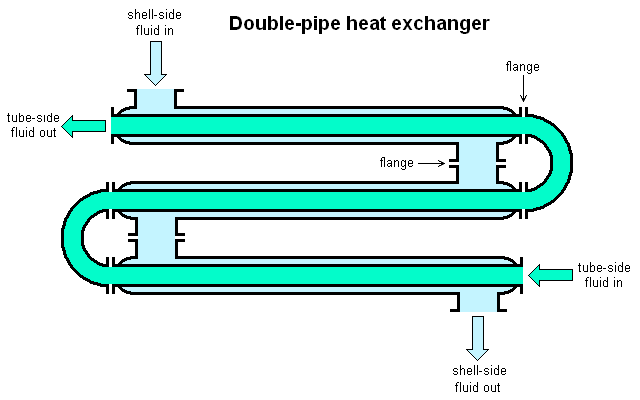
When the above applications for heat exchangers are considered, very quicky, heat exchangers are to become central to the operation of anaerobic digestion processes.
A Quick Anaerobic Digestion Heat Exchanger Guide:
The most common heat exchangers used for anaerobic digestion are shell and tube heat exchangers.
Shell and Tube Heat Exchangers for Anaerobic Digestion Facilities
Concentric Shell and Tube Heat Exchangers are often used to maintain heat in the anaerobic digesters. Sludge from the digester is circulated through the inside tubes of the heat exchanger while hot water is passed through the surrounding outer tube.
Heat exchangers are also designed to warm incoming sludge before it is transferred into the digester. Another application may be for cooling sludge from thermophilic biological processes.
Counter-flow or concurrent flow designs are available.
Full inner tube pipe diameter return bends prevent clogging, reduce head loss, and are fast and easy to remove for service procedures.
Steel or stainless steel concentric tube designs are available.
Galvanized steel or stainless steel insulated panel enclosures are available and have quick-release and re-set latches used for panel removal and easy access to the heat exchanger tubes.
Standard designs allow cleaning of the inner tubes without removing them from the outer tube or the heat exchanger frame.
Where restricted access to the heat exchanger installation point within operations buildings, (perhaps at lower levels in these buildings), OTI can design the heat exchanger in small modules that will fit through these restriction points.
The heat exchangers for anaerobic digestion modules are then assembled, anchored, and connected to plant piping to complete the installation of heat exchangers for anaerobic digestion. via Heat Exchanger | Olympus Technologies, Inc.
Sludge-to-Sludge Heat Exchangers
Almost any Temperature Phased Anaerobic Digestion (TPAD) system offers an opportunity to include a sludge-to-sludge heat exchanger.
The process involves heating sludge to more than 130°F for retention in a thermophilic digester, then cooling the sludge for retention in a conventional mesophilic (less than 120°F) digester.
A sludge-to-sludge heat exchanger is used to remove heat from the thermophilic transfer sludge before it goes to the mesophilic digester. The recovered heat is then used to preheat raw sludge prior to a pass through a water-to-sludge heat exchanger for the thermophilic digester.. via Digester Heating Systems: Heat Exchangers
Spiral Heat Exchangers for Anaerobic Digestion & Renewable Energy
Spiral heat exchangers are a parallel technology to the traditional Concentric Tube Heat Exchangers, and their main supplier says that they excel in sludge heating, cooling, and pasteurization applications.
Their sludge digester heaters are, we are told, serving dozens of small and large communities across North America. Manufacturer Gooch Thermal (US) says that their presence is growing internationally. Gooch Thermal Type 1-DO spiral heat exchangers are designed to maintain the required sludge temperature range in anaerobic digesters for optimal growth of mesophilic and thermophilic bacteria and stabilization of sludge… via Spiral Heat Exchanger | Wastewater Treatment — Gooch Thermal
Biogas CHP
Biologically-derived gases can be utilised in biogas engines to generate renewable power via cogeneration in the form of electricity and heat. The electricity can be used to power the surrounding equipment or exported to the national grid.
Low grade heat from the cooling circuits of the gas engine, typically available as hot water on a 70/90°C flow/return basis. For anaerobic digestion plants that are using a CHP engine, there are two key types of heat:
- High grade heat as engine exhaust gas (typically ~450°C)
The low grade heat is typically used to heat the digester tanks to the optimum temperature for the biological system. Mesophilic anaerobic digesters typically operate at 35-40°C. Thermophilic anaerobic digesters typically operate at a higher temperature between 49-60°C and hence have a higher heating requirement.
High temperature exhaust gas heat can either be used directly into a drier, waste heat boiler or organic rankine cycle unit. Alternatively it can be converted into hot water using a shell and tube exhaust gas heat exchanger to supplement the heat from the engine cooling systems.
Waste heat boilers produce steam typically at 8-15bar. Driers may be useful to reduce the moisture content of the digestate to assist in reducing transportation costs. Organic rankine cycle turbines are able to convert surplus waste heat into additional electrical output.
In the event that the local legislation requires for the destruction of pathogens in the digestate (such as the European Animal By-Products Regulations) there may be the requirement to heat treat the waste via pasteurisation or sterilisation. Here, surplus heat from the gas engine can be used in the pasteurisation unit.
The heat from the CHP engine can also be used to drive an absorption chiller to give a source of cooling, converting the system to a trigeneration plant.
via Biogas | CHP | Cogeneration | Combined heat and power
Other companies in this area, include:
Clarke Energy Anaerobic Digestion / Biogas … Alternatively it can be converted into hot water using a shell and tube exhaust gas heat exchanger to supplement the heat from the … via Biogas | CHP | Cogeneration | Combined heat and power
And,
Evoqua provides a full range of anaerobic … Evoqua is a leader in Anaerobic Digestion … Evoqua also provides digester heaters and heat exchanger … via Anaerobic Digestion – Evoqua Water Technologies
Sludge Heating System Overview: WesTech offers sludge heating solutions for nearly any anaerobic digestion … and heat is transferred within the heat exchanger. via Sludge Heating System – WesTech Engineering, Inc.
Learn how you can utilize sludge heat exchanger solutions from ProSonix. … Slurry & Aggressive Fluid Heating. … Anaerobic digestion of biosolids & wastewater sludges; via Sludge Heat Exchanger for Water + Slurry Heating – ProSonix
Claro – Heat Exchangers/Heat Recovery by Claro Inc. Claro designs and manufactures three proprietary heat exchangers that heat, cool, and recover energy by means of … via Claro – Anaerobic Digestion – Heat Exchangers/Heat …
GE Anaerobic Digestion Technology. Anaerobic technology is a viable way to reduce … Claro designs and manufactures three proprietary heat exchangers that heat, … via Heat exchangers Archives • BiogasWorld
2 BIO-HTX Sludge Heat Exchanger Napier-Reid Ltd. TM Process Anaerobic digestion of sludge converts volatile organic matter to methane and carbon dioxide. via Tube-inTube Counterflow Sludge Heat Exchangers
Shell and tube heat exchangers are recommended for the processing of low, medium, … Shell and Tube Heat Exchangers in Anaerobic Digestion Plants. via Shell and Tube Heat Exchangers – Centri-Force
Monsal’s heat exchangers for anaerobic digestion products include … Heat Exchangers; Compressors; … reliable process equipment and technology to meet your high rate anaerobic digestion … via Biogas, Anaerobic Digestion & Biowaste Energy Solutions …
More information on suppliers is also available at:
Results for sludge heat exchanger equipment … Anaerobic digestion is highly dependent upon … The AAT heat exchanger is used to heat the digester sludge in … via Sludge Heat Exchanger equipment | Environmental XPRT
Scienece Direct confirma our assertion as to the importance of heat transfer in an anaerobic digestion plant in a continental climate context. … Digestion anaerobic heat flow is calculated … Use of a heat exchanger. via Importance of heat transfer in an anaerobic digestion …
Anaerobic digestion … Heat exchangers used to pass the heat from the effluent to the influent are more efficient at the higher … via Anaerobic Digestion Basics – omafra.gov.on.ca
Anaerobic digestion is the process through which … Learn About Biogas Recovery. … Photo of a heat exchanger that works in conjunction with an engine … via Learn About Biogas Recovery | AgSTAR: Biogas Recovery in …
Recent Heat Exchanger Points Made by Matt Hale of HRS Heat Exchangers Ltd
Upgrading an existing plant is an ideal opportunity to improve its overall efficiency and ensure that every bit of heat and power produced is utilised, to maximise both energy production and overall greenhouse gas savings.
The water sector is at the heart of AD efficiency and improvements while the installed capacity for the anaerobic digestion of sewage sludge rose 12% to 2i6MWe between 2010 and 2015, wastewater plants generated more than 25% more power.
Recapturing heat is one of the easiest ways to improve efficiency, and heat exchangers represent the best way of doing this. They are an established technology, but despite their widespread use in industries such as food manufacturing and the chemical sector, they are often under-used in AD plants.
Heat can be utilised in the AD process itself, for example, to pre-heat feedstock or digesters to improve gas production efficiency, or anywhere else that heat is required; from water treatment, pasteurisation and concentration processes to office and space heating, or to provide hot water for cleaning.
Using surplus heat in this way is also free, without the need to buy additional fuel, and all of these applications can be carried out using a suitable heat exchanger.
Such an approach may also provide additional benefits compared to other technologies, such as the tank heating systems often used for pasteurisation.
A well-designed system could recover and utilise 40% of the heat produced by the plant.
As an example, using heat exchangers for pasteurisation is more efficient than using tanks with heating jackets as they have a much lower heat requirement; up to half of that of some systems. This is because tank systems have lower heat transfer efficiency and usually dump the hot water after use, rather than reclaiming it.
Using heat exchangers means that effective pasteurisation of digestate, for example, to comply with PAS 110, is possible using surplus heat rather than needing to install an additional heat source such as a biomass boiler, which could add hundreds of thousands of pounds to a project.
Using a well-designed heat exchanger system can provide a continuous pasteurisation process which uses less energy than alternative systems while allowing additional thermal regeneration, or recovery, levels of up to 6o%. This saved heat can then be used elsewhere, such as an evaporation plant.
Heat can also be used to separate water from digestate by evaporative concentrating. This technique often used with heat exchangers for anaerobic digestion can reduce the overall quantity of digestate by as much as 80%, greatly lowering the transport costs associated with the removal of digestate.
A well-designed system will include measures to retain the valuable nutrients in the digestate while the evaporated water can be condensed and reused. For example, the captured water can be added back to the feedstock as it enters the digester, making the entire process almost self-sufficient in terms of water use and eliminating liquid discharges from the plant.
After concentration, the treated digestate dry solid content can be as much as 20% (often a fourfold improvement), making it easier to transport and handle. A well-designed system could recover and utilise 40% of the heat produced by an AD plant. What could you do with that free heat?
The Concept:
– Using heat exchangers for pasteurisation is more efficient than using tanks with heating jackets
– Using heat exchangers means that effective pasteurisation of digestate is possible using only surplus heat
– Heat can reduce the overall quantity of digestate by as much as 80%
Need to Know:
– The installed capacity for the anaerobic digestion of sewage sludge rose 12% to 216MWe between 2010 and 2015
– The number of sewage biogas plants has – increased from 49 in 2004 to 159 today.
– The Renewables Obligation itself will continue up to 2037
The Verdict
– After concentration, the treated digestate content can be as much as 20% (often a fourfold improvement), making it much easier to transport and handle”
This article was developed from an original article by Matt Hale, of HRS Heat Exchangers
This web page, it consists of valuable Information. Too much heat and we need heat exchangers, not enough (winter time) we need heaters – biogas boilers. Where to buy the biogas boiler? Can you answer please.